The Case for Process Validation
By Mark Land, AAHP President
The Homeopathic Pharmacopoeia of the United States says: “Dosage Forms – These, like all other conditions of homeopathic production should be governed by simplicity and usefulness to the physician and patient.”1
This is a good place to start a discussion about process validation for producing homeopathic drug products. The Pharmacopoeia has contained this aspiration of simplicity since at least the 8th edition and probably longer.2 I argue however that the process of making a homeopathic drug product has never been simple. If we want to achieve the second aspiration, “usefulness to the physician and patient,” process validation is necessary.
There is a mistaken idea that finished product testing makes process validation obsolete. It’s mistaken because finished product testing only addresses the probability that the process achieved its quality goals. Sampling techniques can extend the validity of that probability, but finished product testing is still limited in what it accomplishes. For example, each time there is a failure in a process parameter, the sample size must be increased to account for its recurrence.
Statistical theory aside, validation can improve the reliability of your process and probably save you time and money. Process validation is an intimate study of process variables and their impact on critical quality attributes. Not all variables affect final product quality attributes, and in that way a validation project is about determining what to measure.
A risk assessment is the number of unit operations multiplied by the number of variables within each operation. By that measure, manufacturing a botanical tincture would have about 30 operation/variable parameters (fig. 1).3,4 If we assume roughly the same amount of complexity within the four or so steps to make a tablet product, we come to a complexity value of 120 operation/variable parameters. Simplicity is out the window.
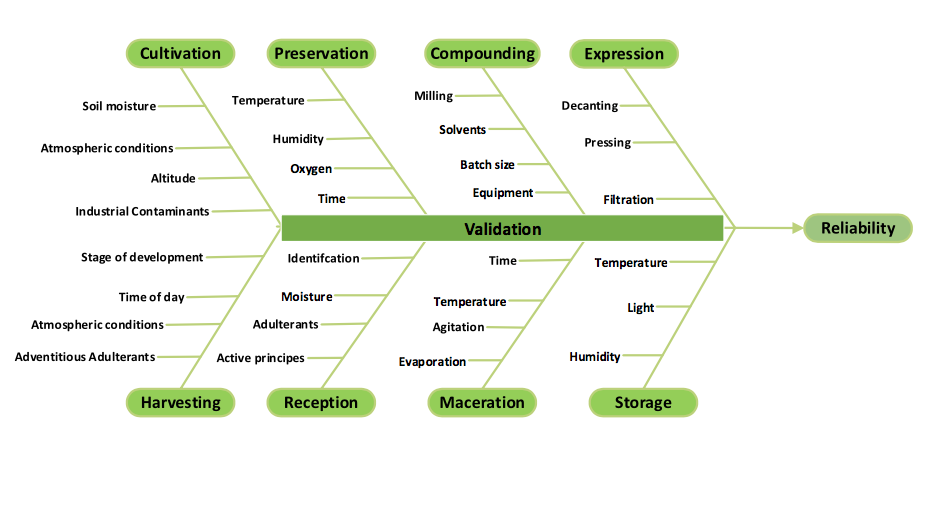
fig. 1
You can image that designing enough experiments to examine all of these parameters is unnecessarily large. It does not have to be that way however. FDA published three guidance documents in the mid-2000s that offer insight into the concepts of Pharmaceutical Development, Quality Risk Management, and The Pharmaceutical Quality System.5 They also published a Questions and Answers guidance that discusses how the three concepts work together to enhance control and quality within the manufacturing environment.
To learn more about process validation, read this article by Pejman Parhami of Hyland’s Inc. Take advantage of his article and FDA’s guidance documents to implement or improve your process validation system.
References:
- Homeopathic Pharmacopoeia of the United States Guidelines for manufacturing homeopathic medicines Section 40 Dosage forms. http://www.hpus.com/online_database/show_file_action.php?GMHM/gmhm-page40.php.
- Homeopathic Pharmacopoeia of the United States 8th edition American Institute of Homeopathy, Falls Church, Virginia; 1979: p 17.
- Homeopathic Pharmacopoeia of the United States Guideline for Manufacturing Homeopathic Medicines Sections 10–24. http://www.hpus.com/online_database/show_file_action.php?GMHM/gmhm-page12.php
- United States Food and Drug Administration Guidance for Industry Botanical Drug Development. https://www.fda.gov/ucm/groups/fdagov-public/@fdagov-drugs-gen/documents/document/ucm458484.pdf.
- United States Food and Drug Administration Guidance for Industry. https://www.fda.gov/RegulatoryInformation/Guidances/default.htm.