The Importance of Standard Operating Procedures
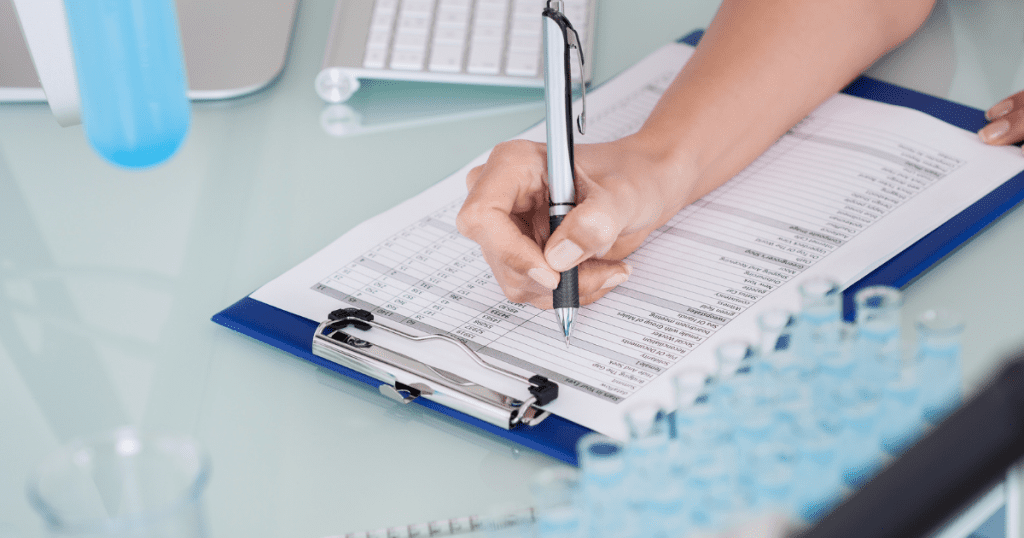
By Mark Land, AAHP President
Manufacturers of health care products rely on precision, rigor and consistency to produce reliable products for patients, physicians and consumers time and again. To drive the kind of culture that consistently and effectively produces results of this nature, companies must first create a culture where quality objectives are transparent, well understood, and acted upon routinely. Standard Operating Procedures (SOPs) are essential for any plant’s effectiveness and efficiency, and they are a regulatory requirement in the pharmaceutical industry.1
The Importance of SOPs
A facility manufacturing pharmaceutical products will typically develop, maintain and execute hundreds of SOPs. This set of written instructions documents a routine or repetitive activity that is followed by employees in an organization. The development and use of SOPs are an integral part of a successful quality system. It provides information to perform a job properly and consistently to achieve pre-determined specification and a quality end-result.
All too often however, processes are not committed to writing or not followed. In fiscal year 2015, FDA cited SOP inadequacy 700 times in six hundred and eighty-three 483s issued to the drug industry in that year.2 Review of outcomes of establishment inspections for labelers of homeopathic drug products FY 2009–2012 revealed 35 of the 93 most frequent 483 citations arose from SOP related problems.3
Content and Format
Properly designed Standard Operating Procedures include step-by-step instructions as well as the following:
- Objective (Purpose)
- Scope
- Responsibilities
- Accountability
- References
- Task Instructions (Procedure)
- Documentation
When generating an SOP, one can choose a number of different ways to organize and format. There are some factors which determine what type of SOP to use or create. (Refer to Table 1.)
- How many decisions will the user need to make during the process?
- How many steps and sub steps are there in the procedure?
Routine procedures that are short and require few decisions can be written in a format of simple steps. Long procedures consisting of more than 10 steps with few decisions should be written along with a graphical format or hierarchical steps. Procedures that require many decisions should be written with an accompanying flow chart.
Table 1: Format Type for SOPs
Does SOP involve many decisions? | Does SOP consist of more than 10 steps? | Best format for writing SOP | Examples |
No | No | Simple sequential steps | SOP for balance calibration |
No | Yes | Sequential steps along with pictorial diagrams | Entry/exit procedure |
Yes | No /Yes | Sequential steps with flow chart | SOP for deviation management |
Writing and Approval of SOPs
SOPs should be written in a concise, step-by-step, easy-to-read format. Each SOP should follow a standard format. Information should be conveyed clearly and explicitly to remove any doubt as to what is required. The active voice and present verb tense should be used. A flow chart should be used to illustrate the process being described.
Documentation should be designed to ensure that steps are followed in a specific order. Any documentation included as part of an activity should be referenced in the procedure where they are to be used and then attached to the SOP. All documentation used during the execution of a procedure becomes part of the batch record file.
Identifying a need, writing and managing Standard Operating Procedures is highly developed within a pharmaceutical company. The organization should have a procedure in place for determining what processes need to be documented. Those SOPs should then be written by individuals knowledgeable with the activity and the organization’s internal structure. These individuals are essentially subject-matter experts who actually perform the work or use the process. A team approach can produce better results.
SOPs should be written by an individual who performs the tasks routinely or someone who is directly responsible for the performance of the task. Ideally SOPs should be written by teams that include some or all of the following people:
- Those who will perform the job;
- Those who will perform maintenance on equipment involved;
- Engineers or others who design equipment and processes;
- Technical initiator;
- Safety personnel;
- Environmental personnel; and
- Equipment manufacturers.
Ideally a writing team should meet at least once in the beginning of a project to establish writing objectives, targets and responsibilities. The team then can work semi-independently with one person serving as coordinator. Write or edit parts of an SOP independently and then one person can combine the individual contributions. Once combined, the draft SOP should be circulated for review among the initiators before editing a final draft for review by supervisors and subsequent supervised testing by employees. Most importantly, SOPs should be reviewed by several people qualified to evaluate the SOP in terms of its completeness and clarity of subject matter. Final approval should be by one or more individuals with appropriate training and experience with the process other than the original writer.
SOP Change Control
To remain current and useful, procedures should be updated when any change occurs in the process. Updated procedures must be re-approved. Modifications should be noted in a change control table in the beginning of an SOP. All versions should receive a unique revision number.
SOPs should be also systematically reviewed on a periodic basis (e.g., every 1–2 years) to ensure that the policies and procedures remain current and appropriate, or to determine whether the SOPs are even needed. The review date should be added to each SOP that has been reviewed. If an SOP describes a process that is no longer followed, that process description should be withdrawn from the current file and archived.
Don’t forget an SOP on preparation, approval, revision and control of Standard Operating Procedures for better control and management of SOPs. The administrative aspects of the SOP system such as distribution and filing should be well managed. Overall system management can benefit from a system owner. Ideally a system owner:
- Eliminates obsolete SOPs;
- Ensures that SOPs meet their quality requirements and are user friendly;
- Manages SOP change controls;
- Distributes SOPs;
- Ensures that SOPs are current;
- Ensures that new or changed SOPs are valid only after training has occurred and provides training about the SOP system;
- Measures system performance and periodically reports results to management; and
- Continuously improves the system.
SOP Implementation
Procedures are not an end in themselves—they do not guarantee good performance or results. More important are well-designed systems and processes, qualified employees, and a motivating company culture. Procedures support process, people and the work environment. However procedures cannot create a good process, a qualified employee, or a positive working environment.
Training is the most important step when implementing an SOP or revision. Training should also include stressing the benefit of following the procedure and risk involved if the procedure is not followed. People are much more apt to follow a procedure when they understand its importance.
SOPs serve as a fundamental means of communication for all levels of the organization. Not only do they involve employees departmentally, but they also allow management and employees to gain a cross-functional view of the organization. This approach encourages employees to think about how process change may affect other functional areas. A good system forces employees to think through processes and examine how procedures might affect product, personnel, production, and equipment. Remember, though, that even the best written SOPs will fail if they are not followed.
Author’s note: This article summarizes an unpublished document originally written by Sanjay Kummar Jain. “Standard operating procedures (SOP) – Back Bone of Pharmaceutical Industries.” Available at https://www.google.com/webhp?sourceid=chrome-instant&ion=1&espv=2&ie=UTF-8#q=importance+of+standard+operating+procedures+Sanjay+Kunner+jain.
1U.S. Food and Drug Administration Code of Federal Regulations Title 21 Food and Drugs Parts 211.
2U.S. Food and Drug Administration FY 2015 Inspectional Observation Summaries. Available at http://www.fda.gov/ICECI/Inspections/ucm481432.htm#Drugs.
3Land, M. Establishment Inspection Outcomes for Labelers of Homeopathic Drug Products, American Association of Homeopathic Pharmacists Network News, June 2016.