An Overview Application of a Quality-by-Design Model for Hahnemannian Dilutions
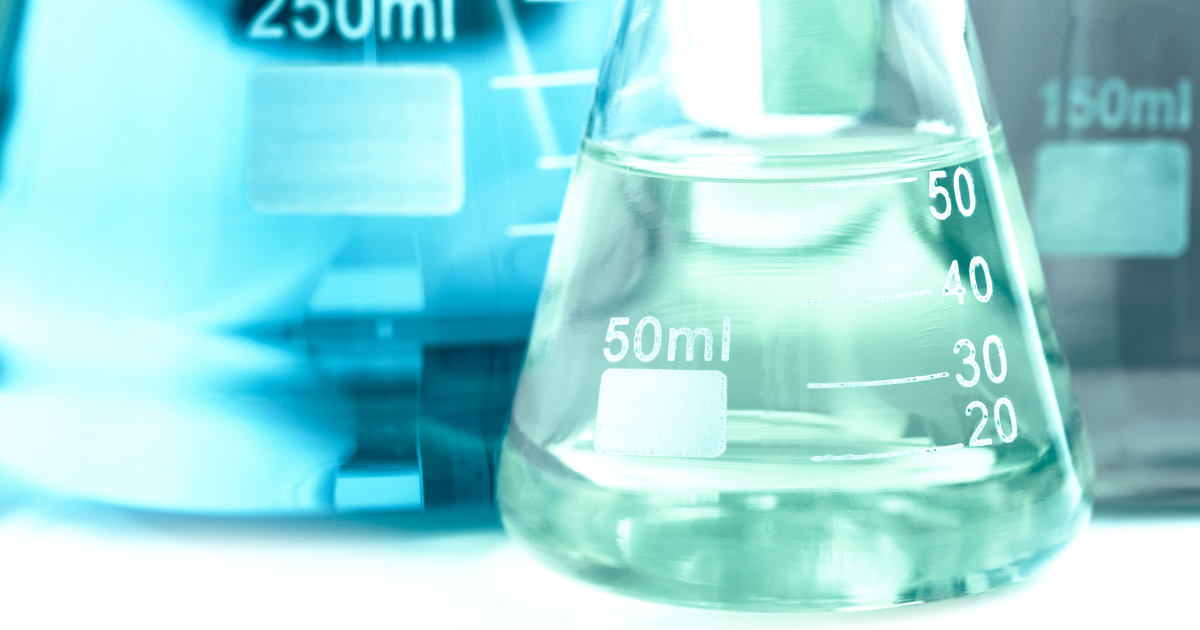
By William Shevin, M.D., President, HPCUS, and Eric L. Foxman, Pharm. (Ret.), Senior Scientist, HPCUS.
The Homeopathic Pharmacopeia Convention of the United States (HPCUS) has made note of current Good Manufacturing Practices (CGMPs) requirements for conventional pharmaceuticals which may be inappropriate or impossible for homeopathic manufacturing to comply with. The basis for this “impossibility” is due to unique aspects of homeopathic drug manufacture.
The HPCUS posted a White Paper1 which “propose[s] science-based methods to achieve compliance… consistent with the spirit of the regulation and the limits of available science.” The paper includes recommendations that meet the needs of both regulators and manufacturers while providing assurances for the former and without placing undue burdens on the latter.
For instance, CGMPs require laboratory determination of the identity and strength of each active ingredient. This can be achieved for homeopathic starting materials and the very lowest attenuations. But what about situations in which an attenuation series begins with an intermediate attenuation? How does a manufacturer achieve compliance when the homeopathic attenuation contains amounts of the homeopathic starting materials which are orders of magnitude below the limits of detection (LOD) of conventional analytical chemistry?
The White Paper describes a “reasonable and attainable alternative” called Quality by Design (QbD), which is based on scientific principles and has been successfully used for more than a decade. QbD has also been the subject of prior FDA guidance. Using a QbD approach, one can achieve “science-based and risk-managed manufacture and distribution of drug products.…”
When it is neither feasible nor practicable to measure the amount of the homeopathic starting material in a homeopathic drug product (HDP), use of a QbD method (which has been specially tailored to address unique attributes of homeopathic practice) can confirm, with reproducible data, that the attenuation process is sufficiently accurate and precise despite containing concentrations too low to measure by conventional means. This method is referred to in the White Paper as Homeopathic Quality by Design (HQbD). It provides a validation of the attenuation process.
When identity testing is impossible due to the ultra-low levels of “testable” substance in the attenuation, validation by HQbD is a reasonable alternative. Such validation assures consumers, healthcare providers, and regulatory authorities that the labeled attenuation will be present in the HDP.
The White Paper discusses the core principles of QbD and their appropriateness for an HQbD model. It also proposes using two specific substances to implement the model for testing levels in successive low homeopathic attenuations to validate the unique homeopathic attenuation process. These were chosen for several reasons: the amounts of each substance are measurable at those attenuation levels, the chemicals are inexpensive, and the test methods are easy to use.
The two compounds can be considered “stand-ins” for most homeopathic starting materials in terms of validating the attenuation process. This “surrogate or stand-in” status is enhanced because one has surface active properties (which may adversely impact predictable quantities in subsequent attenuations) while the other does not. Thus, a side-by-side comparison of each result can further assure proper mixing, dispersal, and de-concentration has been achieved from one attenuation level to the next.
The White Paper suggests through use of an HQbD validation of a company’s attenuation process, the following opportunity is possible: When a supplier provides a buying company with an “untestable” intermediate attenuation (e.g., a 10X which the buying company uses to make a 12X), the supplier will still need to provide a Certificate of Analysis, but must also provide documentation showing the attenuation process has been validated. The HQbD model can be used for that process validation. The buying company will then not need to repeat identity tests on the “untestable” intermediate attenuation2 although they are required to assess the seller’s methods to ensure compliance.
The White Paper recommends such additional documentation should also be available to regulatory authorities in cases where the product is under investigation. Making the documentation available in this manner can actually lessen the overall regulatory burden as it provides meaningful responses to questions which would otherwise be expensive and time consuming to attempt to answer.
The proposed HQbD approach can obviate the need for a manufacturer to test received intermediate attenuations below the LOD, so long as they are accompanied by documentation of the validation described in the HQbD approach. This will eliminate a heavy (and impossible to comply with) burden for companies. Of course, starting materials must still be properly ID tested, the attenuation process must be vigorously validated, and documentation must clearly show all bases have been covered. Limit tests will still need to be performed for intermediates prepared from substances of high toxic concern to confirm these items do not exceed any risk or safety assessments; this provides assurance the product is safe for the consumer even if an undetected manufacturing error has occurred.
References
1. ”Utilizing a Quality by Design Model for Hahnemannian Dilutions in the Manufacture of Homeopathic Drug Products” posted for a 90-day comment period in January 2024. For an electronic copy of the White Paper, please contact info@hpus.com
2. In the given example, such ID tests would simply provide meaningless results because the attenuation is below the LOD.