The Importance of Purified Water Systems in the Pharmaceutical Industry
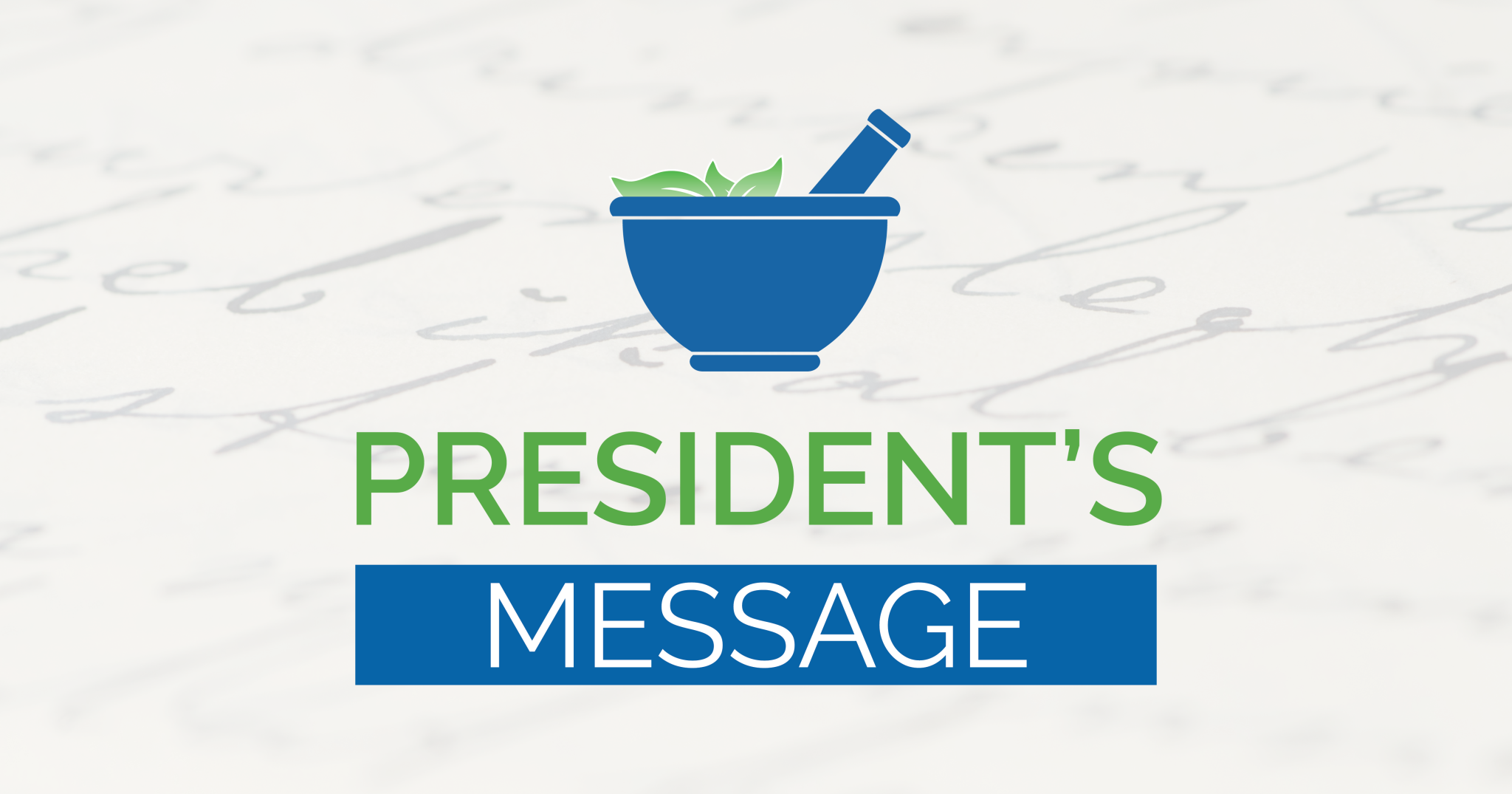
By Mark Land, MS, RAC-US, AAHP President
My first experience with a water treatment system was a double deionization, pre- and post-filtration technique. There was no storage or recirculation. It was to support dishwashing. Later systems became more sophisticated, including recirculation, ultrafiltration, and other decontamination techniques. Even with that, we always bought sterile water processed using reverse osmosis and deionization for use as a component in drug products. This conservative approach was largely out of concern for the chemical purity of the water considering the dilute nature of the homeopathic active ingredients. I was also acutely aware of the overall importance of water in general, considering the variety of roles it plays within the pharmaceutical firm.
Water is the only ingredient that affects every product manufactured in a pharmaceutical facility. Every product has water as a component, intermediate, or process aid in some or several ways. The quality of water available in a pharmaceutical facility is the critical factor in the quality and compliance of a firm’s products.
Pharmaceutical water systems need to do more than provide access to water. They need to provide access to suitable water. The United States Pharmacopoeia (USP) describes eight types of waters. Two are input waters from municipal or onsite sources. Two are waters for pharmaceutical use after treatment of input waters. The other four are packaged waters for use outside of the pharmaceutical manufacturing facility. Of the two process waters, USP purified water is the most ubiquitous within the manufacturing facility.
There are three main processes for producing USP purified water: reverse osmosis, deionization, and distillation. Today nearly all facilities use a combination of at least two of these processes to produce water that meet the requirements of purified water. Processing water to USP specifications is only the first step. Storing, distributing, and dispensing water are important stages in the water’s lifecycle within the manufacturing facility — each with its own challenges.
Storing and distributing purified water within the facility runs risks of microbial and chemical contamination. Managing these risks is critical to the reliability of the water treatment system and, ultimately, the facility in general. Management techniques include both operational and remedial features. Operationally water must be: stored in nonreactive containers; protected from contact with the ambient environment; maintained at an appropriate temperature; and circulated. Remedially water systems must include mechanisms to control and purge microbiological contaminants.
Within a pharmaceutical facility, purified water serves as: a drug substance ingredient or reactant; a component of drug products; a solvent for cleaning drug product contact surfaces; and is used in testing drug substances, products and components. The many purposes of water reinforce the importance of it within the pharmaceutical manufacturing environment.
Failure to maintain the quality of water within the pharmaceutical facility places products and consumers at risk. Your water system will be a focus of an FDA inspection. Problems with your water treatment system will likely result in enforcement actions against all products manufactured in your facility. Know what you need to know. Hire an expert firm to design, install, validate, and maintain your water system.
This vital subject was covered in a June 12, 2024 half-day seminar organized by AAHP during which attendees heard from two FDA officials and two expert consultants.